Surface Mount Technology & Surface Mount Devices, What Are They & How Do They Differentiate?
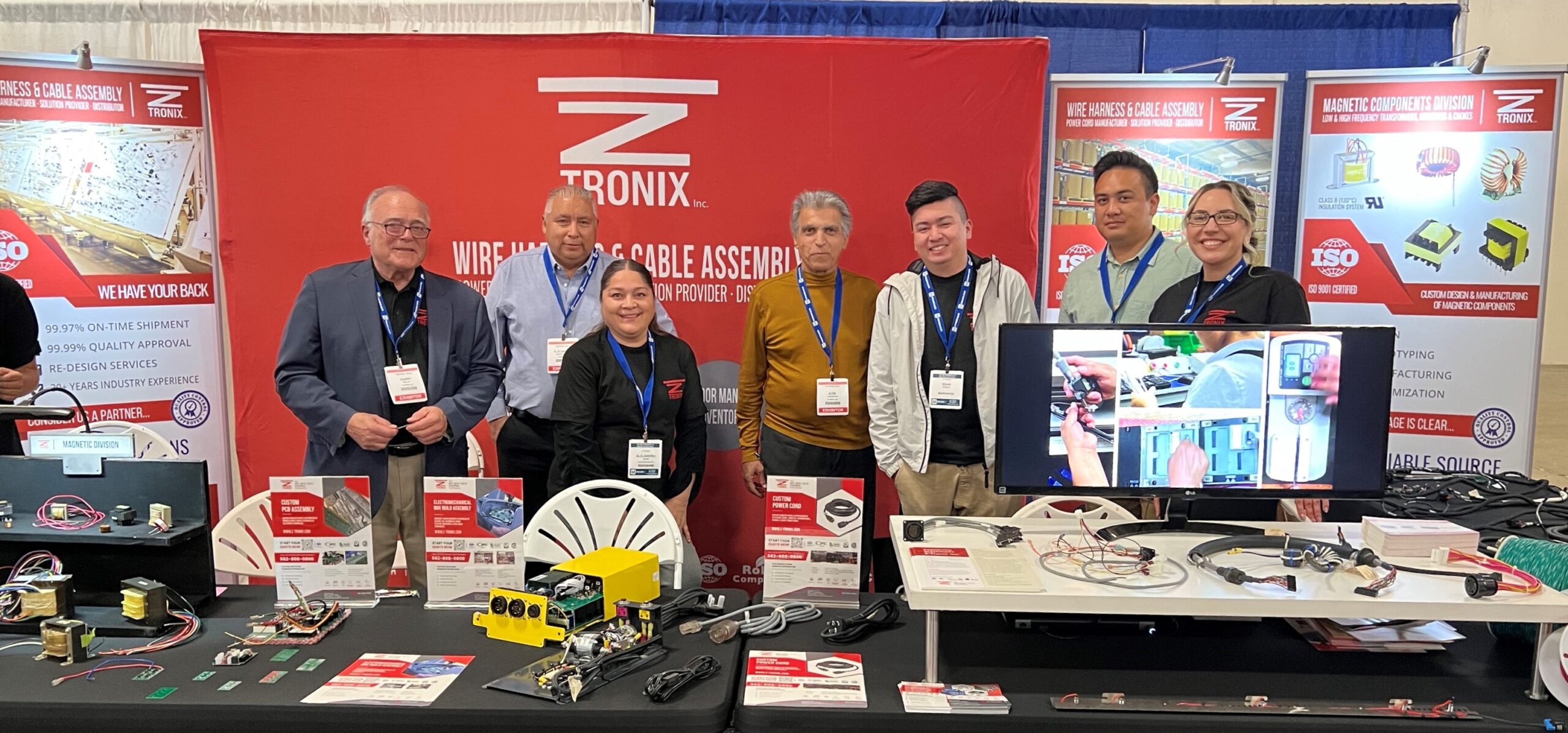
As it is common every year, the Del Mar Electronics & Manufacturing Show (DMEMS) takes place during spring. The show serves multiple functions. One, a place for manufacturers to gather and build relationships with suppliers, and two, a place that assists attendees with the familiarization of new technologies and updated processes. This year during the days of April 24th, 2024 from 10AM to 5PM and April 25th, 2024 from 10AM to 3PM, Z-Tronix Inc. will be making another highly anticipated appearance with a team composed of motivated engineers and experts to assist anyone with questions or seeking electromechanical solutions.
At Z-Tronix Inc.’s combined booths 704 & 706, everyone will be able to get a look at prototypes and samples of electromechanical solutions such as wire harnesses, cable assemblies, power cords, printed circuit board assemblies, electromechanical box build assemblies, magnetic components and raw wire and cable from our distribution division. On top of our manufacturing and distribution services, Z-Tronix Inc. will be highlighting their multiple and diverse vendor manage inventory programs to help customers achieve their lean supply chain objectives.
In addition to the ample range of electromechanical solutions that have positioned us as our customers’ preferred manufacturer for over 35 years; we are pleased to announce the recent addition of industrial control panel assembly manufacturing to our portfolio of manufacturing capabilities.
Z-Tronix Inc. holds exhibitions like these to the highest of regards because our mission motivates us to. Our mission is to attend exhibitions that offer learning opportunities to help build industry knowledge so that we can offer diverse high-quality solutions to our current and potential customers. Additionally, we use exhibitions like these to seek for vendors and suppliers of high-quality raw material that can offer us better terms and pricing with the primary objective of benefiting our customers’ pockets.
Lastly, if you are free during April 24th and 25th, 2024, we highly recommend you visit the DMEMS and stop by Booth 704 & 706 (combined) to learn more about how we can help with your electrical needs. In the meantime, feel free to message us via info@z-tronix.com or call us directly at 562-808-0800!
*FREE ATTENDANCE & FREE ON-SITE PARKING*
Register Here: delreg (manufacturing.show)
2024 Del Mar Electronics and Manufacturing Show address:
Del Mar Fair Grounds
2260 Jimmy Durante Blvd.
Del Mar, CA 92014
Z-Tronix Inc. Booth 704 & 706 (combined)
April 24th, 2024 10AM-5PM and April 26th, 2024 10AM-3PM